What are Traction Motors?
Traction motors are an essential component of locomotives, responsible for converting electrical energy into mechanical power to drive the train. They are the important members of the locomotive electrical parts. These motors play a vital role in providing the necessary traction or pulling force required to move heavy locomotives efficiently. Traction motors are typically electric motors that use various methods to generate rotational force and power. They are designed to operate under the specific conditions and requirements of locomotives, such as high power output, varying speeds, and the ability to handle heavy loads. As the energy source for these motors, both direct current (DC) and alternating current (AC) systems can be used. Traction motors are highly specialized to withstand the demanding operating conditions of locomotives, ensuring optimal performance and reliability.
Locomotive Traction Motors
Locomotive traction motors play a critical role in railway operations by providing power for train propulsion. Essentially, these motors are responsible for converting electrical energy into mechanical energy, allowing trains to move.
Motor failure can have severe consequences for railway operations. Not only can it lead to disruptions in service and delays, but it can also impact the safety and efficiency of train operations. A failed locomotive traction motor can result in reduced power output or even complete loss of propulsion, rendering the train unable to move.
To prevent such issues, regular maintenance and monitoring of locomotive traction motors are crucial. This includes inspections, lubrication, and addressing any identified issues promptly. Additionally, investing in high-quality traction motors and ensuring they are properly installed and integrated into the train’s system can help minimize the risk of failure.
In conclusion, locomotive traction motors are vital components in railway operations, providing the power needed for train propulsion. Understanding their importance and taking proactive measures to prevent motor failure is essential for ensuring the smooth and efficient operation of trains.
Types of Traction Motors
There are several types of traction motors used in locomotives, each with its own unique characteristics and advantages. The most common types of traction motors include direct current (DC) motors, alternating current (AC) motors, and synchronous motors. DC traction motors are widely used in diesel locomotives and electric vehicles due to their simplicity and ability to deliver high torque at low speeds. AC traction motors, on the other hand, are more commonly found in electric locomotives and offer advantages such as higher efficiency, regenerative braking capabilities, and variable frequency control. Synchronous motors are typically used in high-speed applications and provide excellent power density and speed characteristics. The choice of traction motor depends on factors such as customer requirements, operating conditions, and the power supply available.
Direct-Current (DC) Motors
Direct-Current (DC) Motors play a vital role in locomotive traction systems. These motors are commonly used due to their ability to provide high torque at low speeds, making them ideal for starting heavy loads. One type of DC motor frequently utilized in traction applications is the series motor.
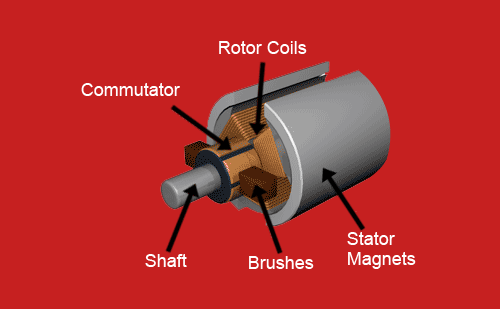
In a DC series motor, the field windings and armature windings are connected in series, allowing the motor to deliver high starting torque. However, the presence of brushes is necessary for the transfer of electrical power between the stationary part and the rotating part of the motor. These brushes require regular maintenance to ensure efficient operation and minimize wear.
While most DC motors have separately excited field windings, where the field current is supplied from an external source, in some cases, reduced field operation is employed. This technique involves reducing the field current during periods of low power demand, improving motor efficiency.
The concept of using brushes in DC motors has been in practice since the 1880s. Though brushes facilitate the transfer of electrical power, they must be monitored and replaced periodically to maintain optimal performance.
In summary, DC traction motors, particularly series motors, are commonly used for their ability to deliver high starting torque. However, their reliance on brushes for power transfer and maintenance requirements should be taken into account during operation. Moreover, the presence of separately excited field windings or reduced field operation can further enhance motor efficiency.

Alternating-Current (AC) Motors
Alternating-Current (AC) motors play a crucial role in locomotive traction systems, providing the necessary power to propel trains forward. These motors are often used in conjunction with variable frequency drives (VFDs), which convert the direct current (DC) output from main alternators into variable frequency AC.
AC motors used in locomotives can be either three-phase induction motors or synchronous motors. Three-phase induction motors are commonly employed due to their robust and reliable performance. These motors are designed to handle the rigorous demands of locomotive applications, providing sufficient torque and power output.
On the other hand, synchronous motors offer certain advantages, especially at low speeds. These motors maintain a constant speed with the rotating magnetic field, resulting in higher efficiency. This makes synchronous motors well-suited for applications where precise speed control and high efficiency are crucial, such as during low-speed operations or starting and stopping locomotives.
The main alternators in locomotives produce DC current, which is then converted into variable frequency AC by VFDs. This allows for greater control and flexibility in adjusting the speed and power output of the AC motors, in response to changing operating conditions and customer requirements.
In conclusion, AC motors, supported by VFDs, are key components in locomotive traction systems. Whether it be three-phase induction motors or synchronous motors, these motors provide the necessary power and control required to propel trains efficiently and reliably.
Universal Motors
Universal motors are another type of motor commonly used in locomotive traction systems. These motors are significant for their versatility, as they can operate on either direct current (DC) or alternating current (AC) power sources, making them suitable for a wide range of applications in trains.
The function of universal motors in locomotive traction systems is to provide the necessary torque and power output to propel the train. They are typically used in lower power applications, such as in light rail systems or smaller locomotives.
Universal motors find applications in various components of locomotive traction systems. They are commonly used in auxiliary systems, such as cooling fans, compressors, or pumps. These motors are also employed in the drive wheels of electric locomotives, contributing to the propulsion of the train.
Key features of universal motors include their compact size, high power-to-weight ratio, and the ability to operate at high rotational speeds. Their versatility in operating on either AC or DC power sources allows for greater flexibility in different locomotive traction systems.
However, universal motors have certain limitations. They tend to have higher maintenance requirements and shorter lifespans compared to other motor types, such as AC or DC motors. Their efficiency can also be lower compared to more specialized motor types designed for specific power needs.
In conclusion, universal motors play a significant role in locomotive traction systems, offering versatility and flexibility in various applications. However, their maintenance needs and lower efficiency should be considered when choosing the appropriate motor for specific locomotive requirements.
Variable Frequency Drive (VFD) Motor Systems
Variable Frequency Drive (VFD) Motor Systems play a crucial role in locomotive traction motors by efficiently controlling torque and speed. Unlike traditional DC motors, VFD systems utilize advancements in microelectronics to provide superior control and flexibility.
In AC motors, the VFD system precisely regulates the frequency and voltage of the electrical input, allowing for accurate control of torque and speed. This is accomplished by converting the incoming AC power to DC using rectifiers. The DC power is then converted back to variable frequency AC using inverters. This conversion process enables the VFD system to match the motor’s power requirements, providing optimal performance and energy efficiency.
The main components of a VFD system include the main alternator, rectifiers, and inverters. The main alternator generates the AC power required by the propulsion system. Rectifiers convert the AC power to DC, while inverters convert the DC power back to variable frequency AC to power the AC motors.
Advancements in microelectronics have made VFD systems easier to control and more efficient than traditional DC motor systems. The precise control of torque and speed, along with the ability to convert DC current to variable frequency AC, allows VFD systems to adapt to changing load conditions and operate at maximum efficiency.
In conclusion, VFD Motor Systems provide optimal control of torque and speed in AC motors, thanks to advancements in microelectronics. Their ability to convert DC current to variable frequency AC enables efficient operation in locomotive traction motors. With their main alternators, rectifiers, and inverters, VFD systems have become essential components in modern locomotives.
Components of a Locomotive Traction Motor System
A locomotive traction motor system is a vital component in diesel-electric locomotives and electric locomotives. It is responsible for providing the power needed for these locomotives to move. The system consists of various components that work together to efficiently convert electrical energy into mechanical motion. Understanding the components of a locomotive traction motor system is essential for ensuring its proper functioning and performance. This article will provide an overview of these components, including the main alternator, rectifiers, and inverters. By exploring how these components work together, we can gain a better understanding of the operation and capabilities of a locomotive traction motor system.
Rotary Converter/Inverter System
The rotary converter/inverter system is an essential component of locomotive traction motors. This system allows for the efficient conversion of power between different forms to drive the locomotive.
In this system, the main alternator generates alternating current (AC), which is then fed into rectifiers. These rectifiers convert the AC current to direct current (DC) to power the locomotive’s traction motors. This DC power is then fed into inverters, which convert it back to variable frequency AC. The variable frequency AC is then supplied to the traction motors, controlling their speed and torque.
The use of alternating current in the overhead wire supply systems has several advantages. Firstly, it enables the use of a rotary converter/inverter system, which offers greater flexibility in power conversion. Additionally, AC power can be transmitted over long distances with less losses compared to DC power. This results in the need for fewer substations and lighter overhead current supply wires.
In conclusion, the rotary converter/inverter system plays a vital role in locomotive traction motors. It allows for the efficient conversion of power from the main alternator to the traction motors through rectifiers and inverters. The use of alternating current in overhead wire supply systems offers numerous advantages, including reduced infrastructure requirements and improved power transmission efficiency.
Magnetic Fields and Armature Design
Magnetic fields play a crucial role in the operation of locomotive traction motors and greatly influence the design of their armatures. The armature, in this context, refers to the rotating part of the motor that interacts with the magnetic fields to convert electrical energy into mechanical energy.
When electric current flows through the armature windings, it generates magnetic fields. These magnetic fields interact with the fixed magnetic fields generated by the motor’s stator, causing the armature to rotate. The direction and strength of the magnetic fields, as well as the design of the armature, determine the motor’s performance and efficiency.
To ensure optimal efficiency and performance, several factors must be considered during the design process. The shape, size, and arrangement of the armature windings should be carefully determined to maximize the magnetic field interaction and minimize losses. The choice of magnetic materials for the core of the armature helps enhance the magnetic field intensity.
Various armature designs are commonly utilized in traction motors. Some involve laminated cores, where thin layers of magnetic material are stacked together, reducing energy losses due to eddy currents. Others employ wound rotors, composed of conductive coils that can be easily controlled to adapt to different speeds and loads.
In conclusion, magnetic fields and armature design are critical aspects of locomotive traction motors. By strategically designing the armature to interact with the magnetic fields, electrical energy can be efficiently converted into mechanical energy, propelling the train forward with maximum performance and efficiency.
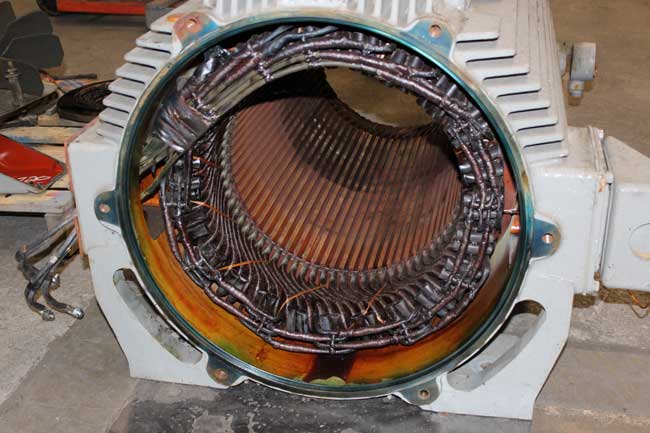
Electrical Wires and Connectors
Electrical wires and connectors play a crucial role in locomotive traction motors by enabling the reliable transmission of electrical power and signals. As vital components of the motor’s electrical system, these wires and connectors ensure the smooth operation and performance of the locomotive.
Proper selection and maintenance of electrical wires and connectors are of utmost importance to ensure the integrity of the motor system. The wires must be chosen based on their current-carrying capacity, voltage rating, and resistance to environmental factors such as heat, vibration, and moisture. High-quality connectors should be selected to provide secure and efficient electrical connections.
Regular inspection and maintenance of these components are essential to avoid electrical failures, reduce downtime, and ensure efficient power transmission. Corrosion, loose connections, or damaged wires can lead to power loss, overheating, or even electrical hazards.
By paying attention to the selection and maintenance of electrical wires and connectors in locomotive traction motors, operators can enjoy the benefits of reliable and efficient power transmission and signal communication. This ensures the smooth operation of the locomotive and minimizes downtime caused by electrical issues.
Engine Power Rating and Output
The engine power rating and output of diesel locomotives play a crucial role in determining their performance and capabilities. Diesel engines are rated based on their operating speeds and output in horsepower.
The rated operating speeds of diesel engines can vary significantly, typically ranging from 350 to 2,000 revolutions per minute (RPM). This variation allows for adapting to different locomotive requirements and operating conditions.
In terms of horsepower, diesel locomotives have a wide range of rated outputs. Most yard-switching and short-haul locomotives are equipped with diesel engines ranging from 600 to 1,800 horsepower. These engines are specifically designed to meet the demands of localized operations.
On the other hand, road units, which are designed for long-haul transportation, commonly feature engines with higher power ratings. These road units typically have diesel engines ranging from 2,000 to 4,000 horsepower, providing the necessary strength and performance for sustained operation over longer distances.
The engine power rating and output of diesel locomotives are crucial factors in meeting customer requirements for hauling capacity and operational efficiency. By selecting the appropriate engine power rating, locomotives can optimize performance while minimizing fuel consumption and emissions.
Power Supply and Level Requirements
Locomotive traction motors require a reliable and efficient power supply to ensure optimal performance. The power level requirements for these motors vary depending on the specific application and locomotive type. In order to meet these requirements, the voltage applied to the motors can be varied using tap changers on transformers.
Tap changers allow for the adjustment of the voltage levels supplied to the motors, helping to minimize energy loss and optimize efficiency. By varying the voltage, the power level can be adjusted to better suit the locomotive’s needs, ensuring smooth and efficient operation.
When it comes to power ratings, locomotive motors operate on 3-phase power and come in a range of capacities. These motors are rated from 11kw to 200kw, providing the necessary power for the locomotive’s propulsion system.
In terms of energy efficiency, it’s essential to use motors that meet the highest standards. Motors classified as IE2, IE3, or IE4 offer improved energy efficiency and can significantly contribute to reducing power consumption and environmental impact.
In summary, locomotive traction motors have specific power supply and level requirements that can be met through the use of tap changers on transformers. These motors operate on 3-phase power and have power ratings ranging from 11kw to 200kw. By utilizing energy-efficient motors, such as those classified as IE2, IE3, or IE4, the overall efficiency and environmental impact of locomotives can be greatly improved.
Advantages of Using Locomotive Traction Motors in North America
Locomotive traction motors offer numerous advantages in the context of North America’s railway systems. These motors play a crucial role in the propulsion and efficient operation of diesel-electric locomotives. One significant advantage of using locomotive traction motors is their ability to provide high levels of torque, allowing trains to start and accelerate smoothly. Additionally, these motors offer excellent speed control, allowing for precise adjustments to match the operating conditions and optimize performance. Another advantage is the ability to utilize regenerative braking, which converts the kinetic energy of the moving train into electrical energy, reducing wear on the mechanical braking systems and improving overall energy efficiency. Moreover, locomotive traction motors are designed to withstand the harsh operating conditions commonly found in North America, including extreme temperatures, heavy loads, and varying terrains. With their proven reliability and durability, these motors ensure the safe and uninterrupted transportation of goods and passengers. Overall, the use of locomotive traction motors in North America brings several advantages, including improved performance, energy efficiency, and reliability, contributing to the efficiency and sustainability of the region’s railway systems.
Improved Performance and Energy Efficiency
Locomotive traction motors have revolutionized the railway industry by offering improved performance and energy efficiency compared to traditional steam locomotives. These advanced motors provide several advantages, including enhanced maintenance, fuel efficiency, acceleration, and reduced track damage.
In terms of maintenance, locomotive traction motors require less frequent servicing and have longer lifespans compared to steam locomotives. This is due to their simplified design and fewer moving parts, resulting in reduced maintenance costs for railways.
Furthermore, traction motors contribute to increased fuel efficiency, making them more cost-effective and environmentally friendly. Their ability to control power output allows for optimal fuel consumption, resulting in significant savings for railroad companies.
Acceleration is another area where locomotive traction motors excel. The instant torque provided by these motors allows for quick and efficient acceleration, improving overall train performance and reducing travel times.
Moreover, the use of locomotive traction motors minimizes track damage. With their precise speed control and reduced wheel slippage, these motors exert less strain on tracks, resulting in reduced wear and tear and extended track lifespan.
Finally, locomotive traction motors offer greater operating flexibility. They can operate on various terrains and gradients, making them suitable for a wide range of railway lines with different requirements.
Overall, locomotive traction motors provide improved performance and energy efficiency, making them a superior choice over traditional steam locomotives. Their enhanced maintenance, fuel efficiency, acceleration, reduced track damage, and operating flexibility contribute to a more cost-effective and sustainable railway system.
Read this for step-by-step instructions on GE locomotive traction motor repair.